Understanding the Landscape of Plastic Mold China
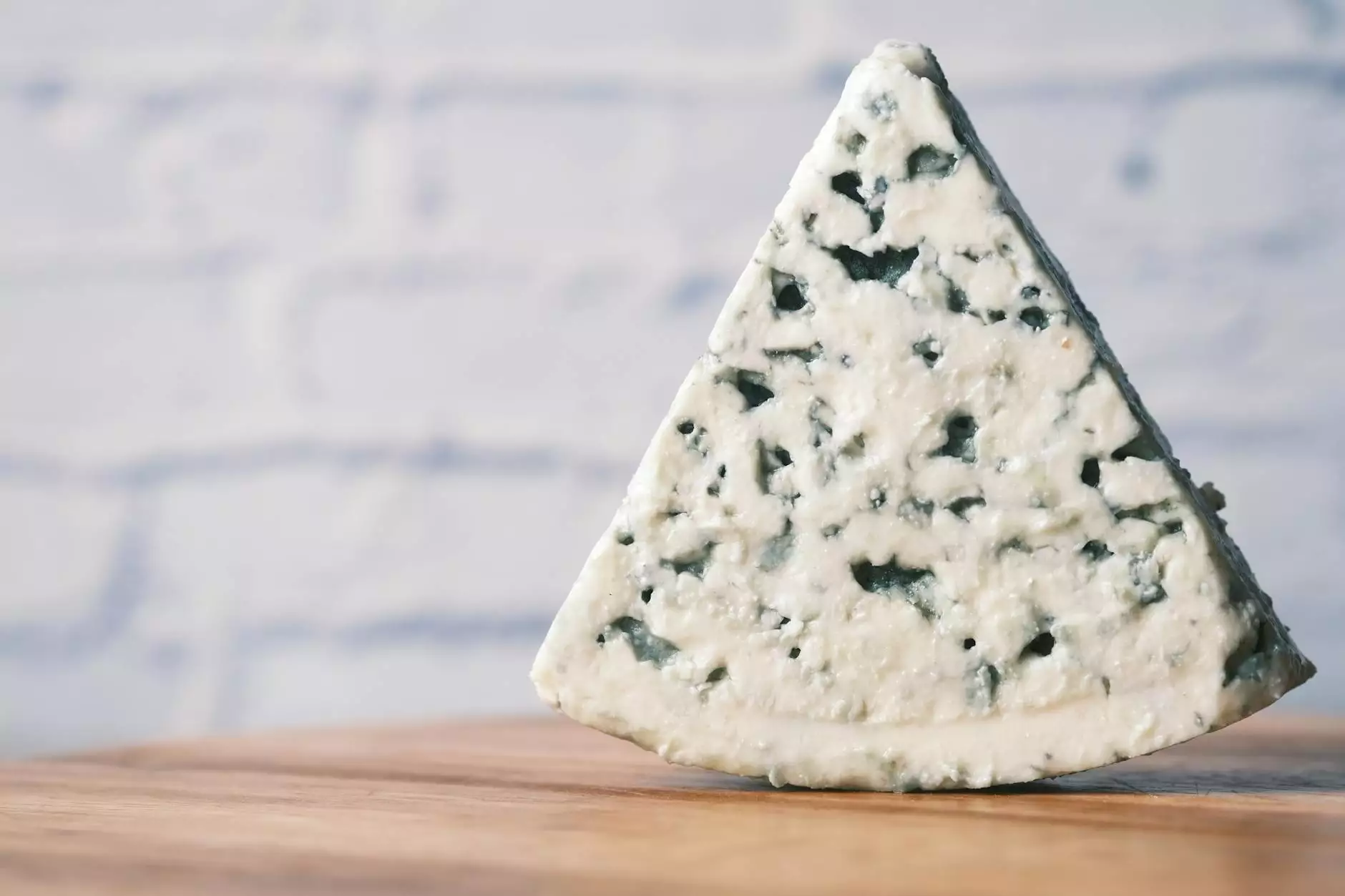
The field of plastic mold manufacturing in China has evolved remarkably over the last few decades. As global demand for high-quality plastics continues to rise, China's position as a leader in this industry is firmly established. In this article, we will explore the ins and outs of the plastic mold industry in China, examining its advantages, production processes, technologies, and the future outlook.
Why Choose China for Plastic Mold Manufacturing?
China has become the go-to destination for businesses looking for reliable and cost-effective plastic mold manufacturing solutions. Below are some compelling reasons why outsourcing mold production to China could be a strategic move for your business:
- Cost Efficiency: The labor cost in China is significantly lower than in many Western countries, allowing businesses to save money while maintaining quality.
- Advanced Technology: Chinese manufacturers have access to cutting-edge technology and machinery, which enhances the precision and efficiency of mold production.
- Skilled Labor: With decades of experience in manufacturing, China boasts a workforce skilled in the art of mold making.
- Robust Supply Chain: The extensive network of suppliers and manufacturers in China ensures a smooth and efficient production process.
- Rapid Prototyping: The ability to quickly produce prototypes allows businesses to test and iterate their designs faster, reducing time to market.
The Plastic Mold Manufacturing Process
Understanding the plastic mold manufacturing process is crucial for businesses aiming to leverage this industry for their needs. Here’s a detailed breakdown:
1. Design and Engineering
The first step in creating a plastic mold is to design the product. This stage involves:
- CAD Modeling: Designers use Computer-Aided Design (CAD) software to create 3D models of the product, ensuring accuracy and functionality.
- Material Selection: Choosing the right materials is essential for durability and performance; common choices include aluminum and steel.
2. Prototype Development
Once the design is finalized, a prototype is developed. This step includes:
- 3D Printing: Many manufacturers utilize 3D printing to create prototypes, which allows for quick adjustments and testing.
- Testing and Validation: Prototypes are tested for functionality and precision, ensuring that the final product meets quality standards.
3. Mold Fabrication
After validation, the actual mold is fabricated through processes such as:
- CNC Machining: Computer Numerical Control (CNC) machines are used to cut and shape the mold from metal blocks with high precision.
- Surface Treatment: Molds undergo surface treatment to improve durability and finish quality.
4. Injection Molding
The final stage is injection molding, where:
- Material Injection: Plastic is injected into the mold under high pressure to form the desired shape.
- Cooling: The mold is cooled to allow the plastic to solidify before being ejected.
Key Technologies in Plastic Mold Manufacturing
China is at the forefront of technological advancements in mold manufacturing. Some key technologies include:
- Multi-Cavity Molds: These molds have multiple cavities, allowing for mass production of identical parts in one cycle.
- Hot Runner Systems: They improve efficiency by maintaining the plastic in a molten state to reduce waste.
- 3D Printing for Molds: This cutting-edge technology allows for rapid prototyping and more complex designs.
The Future of Plastic Mold Manufacturing in China
The future of the plastic mold industry in China looks promising due to several factors:
Growing Demand
The increasing demand for plastics across various sectors such as automotive, consumer products, and electronics fuels growth.
Sustainability Initiatives
As global awareness about environmental issues rises, Chinese manufacturers are adopting sustainable practices in mold making. This includes the use of recycled materials and energy-efficient processes.
Government Support
The Chinese government has implemented policies to support manufacturing and technological innovation, providing a favorable environment for growth.
Challenges and Considerations
While the opportunities are abundant, navigating the plastic mold industry in China does come with challenges:
- Quality Control: Ensuring consistent product quality can be challenging; thus, selecting a reputable manufacturer is crucial.
- Communication Barriers: Language and cultural differences can lead to misunderstandings, making clear communication essential.
- Intellectual Property Risks: Protecting your designs and innovations is vital when collaborating with foreign manufacturers.
Choosing the Right Manufacturer in China
To fully capitalize on the benefits of plastic mold manufacturing in China, selecting the right manufacturer is paramount. Here are some tips:
- Research Reputation: Look for reviews, case studies, and testimonials to understand the manufacturer's reliability.
- Request Samples: Before making a commitment, ask for samples to evaluate the quality of their work.
- Assess Communication: Ensure that the manufacturer can effectively communicate in your preferred language and understands your requirements.
Conclusion: Embracing the Future of Plastic Mold Manufacturing
The landscape of plastic mold manufacturing in China provides a wealth of opportunities for businesses worldwide. With a robust supply chain, advanced technology, and a skilled workforce, China stands as a beacon in the global manufacturing sector. Although challenges exist, diligently choosing the right manufacturing partner will enable businesses to navigate this vibrant market successfully.
In conclusion, the potential for growth, innovation, and cost-saving in the plastic mold industry in China is immense. As you consider expanding your operations or improving your production processes, think about the transformative possibilities that China’s plastic mold manufacturing offers.
plastic mold china