The Comprehensive Guide to Molding Plastic Injection in Metal Fabrication
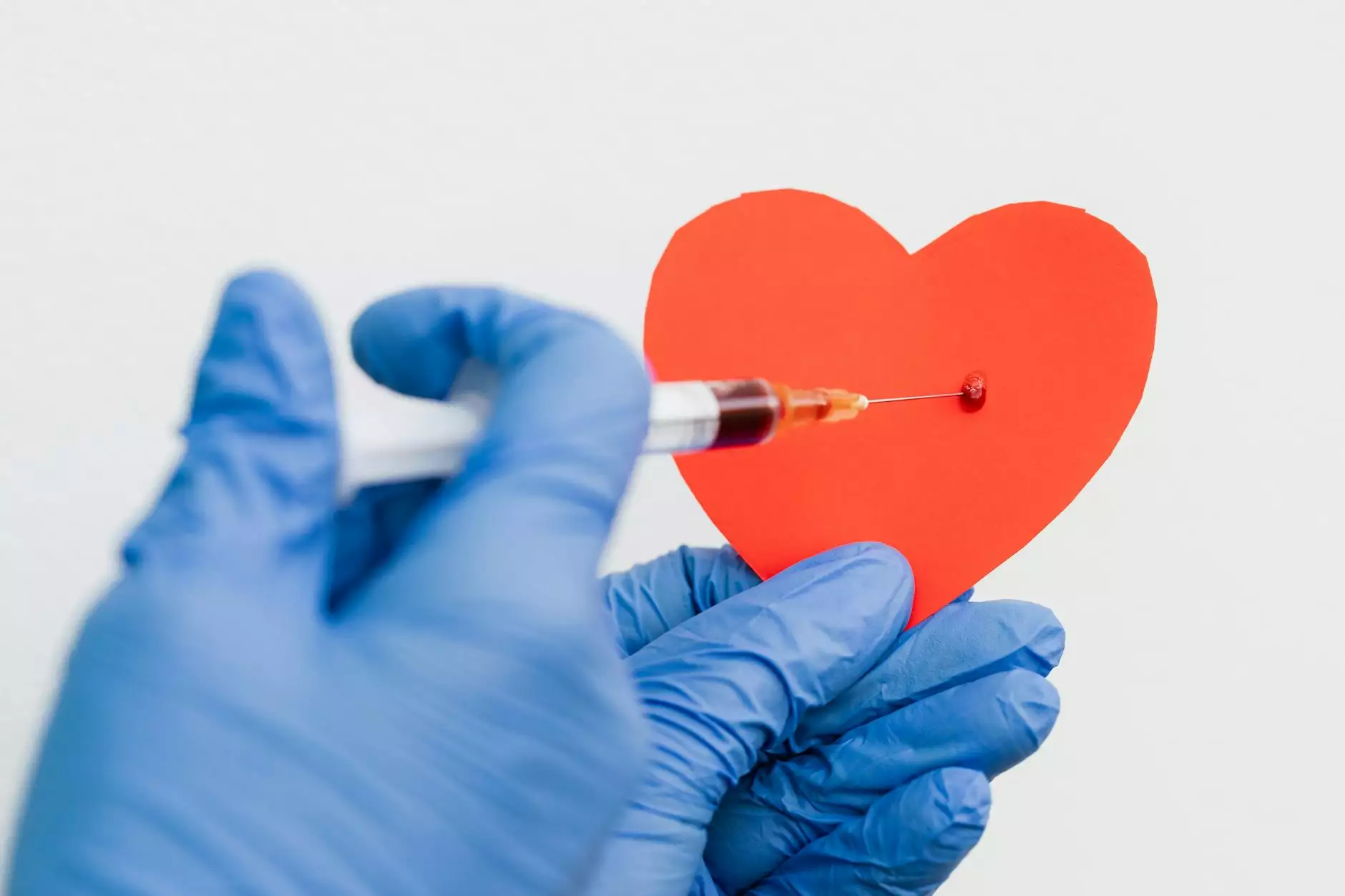
Introduction to Molding Plastic Injection
Molding plastic injection is a revolutionary manufacturing process that has transformed industries by providing high-quality, durable components at an efficient rate. This process is particularly significant in the realm of metal fabricators, where precision and reliability are paramount. At DeepMould.net, we want to highlight how this technique can elevate your operations and expand your capabilities.
What is Molding Plastic Injection?
Molding plastic injection involves injecting molten plastic into a mold where it cools and solidifies to form precise shapes. This process offers a variety of benefits, including:
- High Efficiency: The speed of production significantly reduces labor costs and time.
- Complex Shapes: Capable of producing intricate designs that are difficult to achieve with other manufacturing methods.
- Material Versatility: A wide range of plastics can be used, allowing for tailored solutions.
- Low Waste Production: The process minimizes waste by using only the required amount of material.
The Process of Molding Plastic Injection
The injection molding process can be broken down into several crucial steps:
1. Mold Design
The design of the mold is pivotal. It must be meticulously crafted to meet the specifications of the product you want to produce. Factors such as material selection, size, and shape are carefully considered.
2. Material Preparation
The selected plastic material is then prepared by heating it to a suitable temperature, allowing it to flow easily into the mold cavity. This preparation is vital to ensure that the material reaches its desired properties.
3. Injection Phase
Once the material is prepared, it is injected into the mold under high pressure. This phase ensures that the molten plastic fills every cavity of the mold and takes its shape precisely.
4. Cooling Time
After the injection, the material must cool down and harden. This step can take varying amounts of time depending on the material and mold design. Proper cooling is crucial to avoid defects in the final product.
5. Ejection of the Product
Once the product has hardened, it is ejected from the mold. This step requires precision to avoid damaging the product or the mold. The finished piece is then inspected for quality.
Advantages of Molding Plastic Injection for Metal Fabricators
For metal fabricators, incorporating molding plastic injection into their processes can provide numerous advantages:
1. Cost-Effectiveness
Utilizing molding plastic injection can drastically reduce production costs. The efficiency of the process allows for mass production of parts, thus minimizing the cost per unit. This is particularly beneficial for businesses looking to increase their output without a proportional rise in expenses.
2. Enhanced Product Quality
Products produced through molding plastic injection are typically of higher quality due to the consistent manufacturing process. The precision offered allows for tight tolerances and high accuracy, which is essential in metal fabrication where components must fit perfectly.
3. Reduction of Lead Times
The rapid turnaround time of molding plastic injection means that products can be made faster, which helps businesses respond to market demands much more swiftly. This agility is crucial in maintaining competitive advantage in today’s fast-paced environment.
4. Environmental Sustainability
With increasing pressure on businesses to adopt sustainable practices, molding plastic injection proves beneficial by producing less waste and allowing for recycling of materials, thus contributing to eco-friendly manufacturing.
Applications of Molding Plastic Injection in Metal Fabrication
The applications of molding plastic injection in the field of metal fabrication are extensive. Some of the notable areas include:
- Automotive Components: Manufacturing parts like dashboards, trims, and even enclosures for electronic systems.
- Construction Industry: Creating durable and lightweight components such as fixtures and fittings.
- Electronics: Producing housings and body parts for devices ranging from smartphones to industrial machinery.
- Consumer Products: From household items to personal devices, molding plastic injection delivers high-quality consumer products.
Choosing the Right Partner for Molding Plastic Injection
To maximize the benefits of molding plastic injection, it is crucial to choose the right partner. Here are some key considerations:
1. Expertise and Experience
Look for companies that have extensive experience in molding plastic injection and have a strong portfolio. Their expertise can guide you through the intricacies of the process, ensuring top-notch results.
2. Advanced Technology
Working with a partner who employs cutting-edge technology can greatly enhance the quality and efficiency of production. Advanced machines and techniques minimize defects and improve turnaround times.
3. Customization Capabilities
The ability to customize designs and adjust to specific requirements is essential. A proficient molding plastic injection partner should offer tailored solutions to meet your individual needs.
4. Quality Control Measures
Choosing a manufacturer with rigorous quality control processes ensures that every produced part meets the highest standards of excellence.
Conclusion
Molding plastic injection is a cornerstone of modern manufacturing, particularly within the realm of metal fabrication. By understanding its processes, advantages, and applications, businesses can significantly enhance their production capabilities and efficiency. At DeepMould.net, we are committed to providing top-notch solutions to meet your molding plastic injection needs. Embrace the future of manufacturing by integrating this innovative technique into your operations today.
Contact Us
If you are interested in exploring molding plastic injection for your business, feel free to contact us. Our team is ready to assist you in achieving your production goals and driving your business forward.